CHAPTER ONE
INTRODUCTION
The construction of a two-face gas burner as a project topic that
we embark upon become necessary as a way of way of putting into
application the engineering and technological knowledge acquired so far.
It is a starting point of actualizing a functional technology in the
country. Irrespective of the fact that there are several breads of gas
burners in the market, especially the ones imported, we deemed it
necessary to work further on it as a way of modifying the brand with
cast not left out in such modification.
1.2 LITERATURE REVIEW
The development of simple
gas burner started in the eighteen countries when people began to use
coal gas for burning. The application was fast put into practice by
William Mulock who designed the simple gas cooker to be used in his
office, home and workplace
The first experimental gas cooker was made and in use in 1850. The
improvement of this has multiplied greatly and is up to date widely
used in homes, restaurants and large catering establishments. The
different types of gas cookers available in the in the market are based
on skills and techniques of the designer or producer.
Based on the nature of energy supply, some gas cookers are made up
of combustion devices of an electric heating element. The
well-constructed ones are properly adapted and form an integral
combustion of which of which they generate and utilize heat. It is often
quite different to draw a line where heat generation stops and where
heat utilization starts in a fuel forced cooker. That is the fuel fired
cooker being on the pack in the market these days.
The releasing of heart starts with mixture of air and fuel gas in
the nozzle and combustion of the mixture to release heart takes place
at the burner.
1.3 SPECIFICATION OF PROBLEM
In the course of fabricating the two-face gas burner, as a copied
project with some propose modification, some condition which ought to
be met are found as a standard of comparison with the already existing
ones. This posed a difficulty in the course of this construction. Since
choice between already existing gas cooker lies on service available,
durability, connivance cost.
The following specifications were considered a problem when we started the design.
- PORTABILITY.
How to fabricate a two-face gas burner that will occupy the
minimum space in the kitchen was a problem. A two-face gas burner that
is easily to be met in met in our design.
- To construct a two-face gas burner that will be safe to any prospective user.
- To constructs a two-face gas burner that will be easy to maintain and wise gas will be free from unpleasant smell.
- To construct a two-face gas burner whose source of energy (fuel) will be local.
- COMPONENT PARTS AND THEIR FUNCTIONS
- Burner chamber
- Linkage pipe
- Hose
- Gas Cylinder (containing gas valve)
- Angle bar (material)
- Control knob or valve
- Connection pipe for gas flow
- Nut
- Rod.
THE BURNER: This being the main component where
combustion takes place to release heat. There is gas delivery line,
which leads to it in addition to an adjustment to control the rate of
atmospheric air mixing with the natural gas
LINKAGE PILE: This is the pipe line through which natural gas flow to the burner. One is lined along the frame of the burner as seen.
THE GAS CYLINDER: This is the
component of the gas burner that containing the gas fuel through which a
hose as connected to the copper pipe of the burner through the gas
passes to the burner for combustion.
THE ANGLE BAR: This was used in constructing the frame of the gas burner.
HOSE: This serves as a link between the copper tubing and the control value of the burner.
CONTROL KNOB OR VALVE: It
is a essential component of the gas burner and it is used to regulate
the volume or amount of natural gas flowing to the burner.
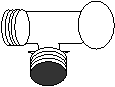
MILD STELL PLATE this is used as a covering or a wall for the gas burner. It also serves as a seat for the values.
CHAPTER TWO
COMBUSTION MECHANISM/THEORY OF THE GAS BURNER
- DESCRIPTION OF COMBUSTION DEVICE.
There are different types of commercially fixed gas
burner and combustion equipment in which usage. Some knowledge of this
type of burner, combustion and aerodynamics within a plant is therefore
essential if a physical study is to be a success.
The combustion equipment is usually selected to satisfy a
range of design requirement including firmly rate, flame length and
shape, temperature and combustion product. All these factors influence
the heat transfer, hence the thermal efficiency of the burner in a
particular and on the nature on its aerodynamics behaviour when
installed in plant.
In practice, many burner fall into categories which has deterring implication
2.2 PRE-MIX OR NOZZLE AIR BAST BURNER
In both cases, flame
stabilization is commonly achieved by employing a refractory tunnel
downstream at the burner head with combustion substantially completed
within the tunnel. This